Refinery
Chemical Cleaning of Fouled Fluidized Catalytic Cracking Unit
Cracking is the process in which large hydrocarbon molecules break into smaller molecules. In a fluidized catalytic cracking unit, fouling generally occurs in the fractionation towers and the slurry loop. This can be resolved using solvents, degassing, and decontamination chemicals.

Chemicals Utilized
FCCU Process
The fluidized catalytic cracking unit (FCCU) consists of three processes. Of course, the purpose of the FCCU process series is to increase the volume of gasoline range liquids. This is because the final products are more valuable than the high-boiling, high-molecular hydrocarbons that enter this process.
1
Firstly, during the reaction step hydrocarbon heats to a high temperature. And, it comes in contact with the catalyst. Then, a cracking reaction takes place. At the same time, coke forms.
2
Secondly, is the catalyst regeneration step. By burning the coke that forms, regeneration of the catalyst occurs. In other words, the catalyst can promote a cracking reaction. There are three basic types of catalytic crackers.
Fluid Bed Style
To start with, the fluid bed is the most popular bed design. Furthermore, the catalyst is a powder in this case. And, it is fluidized with air or hydrocarbon vapor.
Moving Bed
Next, moving beds have beads or pellets as the catalyst. Yet, in this case a mechanical process moves the catalyst.
Fixed Bed
Then, the fixed bed has a series of bed reactors. Usually, only one bed is in operation at a time. And, during this time the regeneration of the other bed occurs.
3
Thirdly, is the fractionation of the cracked products. The cracked hydrocarbon vapor exits the reactor into the fractionator. Finally, the distillation of products into end products occurs.
What Problems do the FCCU Cause?
In general, the fouled fluidized catalytic cracking components are the fractionation towers. Also, associated heat exchangers, coolers and piping can also become fouled. Usually, there is no chemical cleaning of reaction and regeneration components.
Similarly, the FCCU fractionator requires periodic decontamination of oils, varnishes and LEL vapors when compared to other fractionators in the refinery. In addition, the bottom of the fractionator, the heat exchangers, fin-fan coolers, water-cooled exchangers and the slurry settler will have heavy organic fouling.
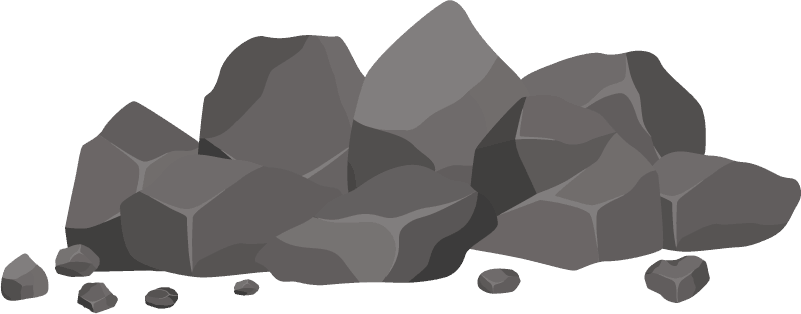
Our Chemical Cleaning Solution
The fouled fluidized catalytic cracking unit will undergo degassing and decontamination during a shutdown. As a result, the units are safe.
1
Dissolve Heavy Waxes, Tars and Asphalt
To begin, FQE® Solvent-H+ is used to remove the heavy organics from the main fractionator. Also, application through the circulation loop ensures removal of contaminants from the exchangers and the slurry settler.
2
Degrease Unit
Next, use one of the specialized FQE Degreaser chemistries to degrease the finfan coolers.
3
Decontaminate Gases
Finally, the main fractionator and side separation towers are degassed and decontaminated with a mixture of FQE LEL-Vapor, LEL-Surface, and FQE Pyrophoric.