Contaminants
Pyrophoric Iron
Iron sulfide deposits are a flammable hazard that occurs in processing equipment, such as filters, and will spontaneously combust when it comes in contact with air.
Why is Pyrophoric Iron a problem?
Controlling Pyrophoric Iron
Current Industry Practices
What is Pyrophoric Iron?
Pyrophoric Iron (FeS) is a form of iron sulfide that combusts on exposure to oxygen; in this case with air. It is formed by reaction of hydrogen sulfide with carbon steel. The iron in the steel reacts with hydrogen sulfide to create an iron crust scale on the metal surface. When a refinery processes sour crude oil, the hydrogen sulfide present in the crude oil causes this problem to develop. When production stops for maintenance work, any iron sulfide present can react with the air through an oxidation reaction.
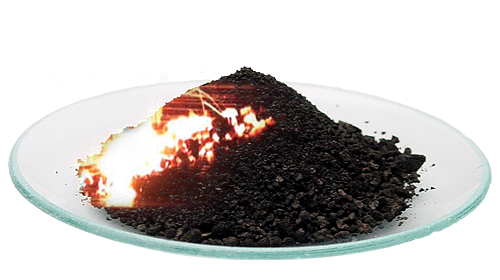
Why is Pyrophoric Iron a problem?
The oxidation of the sulfide anion by the oxygen in the air releases a tremendous amount of heat. The amount of heat can be enough to make the iron deposits glow red. While the iron itself cannot catch fire, if there is a fuel source present (e.g., residual oils, hydrocarbon gases), the heat created is adequate to ignite the fuel source, and fire must be avoided at all costs.
Pyrophoric Iron Control with
FQE® Pyrophoric
FQE Pyrophoric is a water-based product designed to control the combustion of iron sulfide deposits. This is accomplished in a unconventional way: by preventing oxidation.
As previously stated, pyrophoric iron combusts at high temperatures due to the heat of oxidation. In many cases, the customer is not concerned about removing the iron sulfide deposits from the equipment. The iron scale is actually a protective layer that inhibits further metal corrosion, but the industry only knew two methods for controlling FeS before FQE Pyrophoric.
Our method involves using proprietary chemistry to prevent oxidation by blocking the sulfide reaction sites. The inhibition is almost immediate on contact between the pyrophoric product and the iron sulfide scale.
FQE Pyrophoric is chemically compatible with the other degassing chemical products offered by FQE and is nonreactive in those chemistries. As a result, we can perform a steam-phase degassing job and add in FQE Pyrophoric two hours before the end of the steaming process to completely eliminate any iron oxidation concerns. The process of controlling FeS combustion is simultaneous with degassing, degreasing, and hydrogen sulfide control.
The Benefits of Using FQE Pyrophoric:
1
No handling of hazardous chemicals like sulfuric acid or potassium permanganate
2
No solids management
3
No generation of large amounts of hydrogen sulfide
4
No excessive waste water volumes for disposal
5
No hold-ups in waste water disposal for pH adjustments
6
No extended down time for slow reactions or slow chemical addition rates
And most importantly, no more lost production time to manage iron sulfide. This is extra revenue for the refinery; hundreds of thousands of dollars
Industry Practices for Controlling Pyrophoric Iron
One practice used in the oil industry to address pyrophoric iron is to destroy the iron deposits by adding either hydrochloric or sulfuric acid to the cleaning process steps following degassing and degreasing of the equipment. By adding the acid, large amounts of hydrogen sulfide are produced that must be controlled for safety concerns. This is typically accomplished by the addition of a product called Glyoxal.
The acidification practice is slow and is controlled time-wise to manage temperature and metal corrosion rates. The waste fluids must be neutralized before the waste water can be disposed. While the industry is well practised in the use of acids for this process, the acids are potentially hazardous to human health and require careful to handling
Additionally, this process often results in solids that must be managed and disposed of.
Acidification equals:
- Handling hazardous chemicals with the acids
- Extended processing times to control heat and corrosion rates
- Generation of large amounts of hazardous hydrogen sulfide gas
- Requirement for control of generated H2S
One common way of dealing with pyrophoric iron is to intentionally oxidize the sulfide anion into the sulfate by adding caustic permanganate. Potassium permanganate is a strong oxidizing agent, and the oxidation is catalyzed with caustic soda. This is the same oxidation reaction of oxygen with iron sulfide that already causes so much concern. The permanganate oxidation process is very slow by design and is conducted like acidification: after the vessel is degassed and degreased. Again, the heat of oxidation must be carefully controlled to avoid a potential fire, as there is almost always some amount of organic material still in the vessel while this process is taking place.
This step of decontamination for control of pyrophoric iron can take 1-3 days to complete. It continues until the permanganate solution turns from purple to brown. The colour is typically used as the point of completion, though the colour change in itself is not definitive, as no one knows how much FeS is present. A colour change simply means that the permanganate is spent and cannot oxidize more existing iron sulfide deposits. For this reason, the industry continues to add more permanganate after the initial colour change to hopefully insure all of the FeS has been oxidized.
In reaction with iron sulfide, permanganate creates an abundance of manganese dioxide solids. Every project that uses permanganate must manage a lot of these brown solids. They typically require a lot of water flushing to remove the solids from the vessel. The solids disposal is another cost to the refiner.
Permanganate oxidation equals:
- Extended processing times; by extra days and not hours
- Hazardous chemical operations to control heat and rate of reactions
- An abundance of manganese dioxide solids for disposal
- Large volumes of water for disposal
- Big chemical cost as KMnO4Â is expensive