Part 17
Petroleum refining catalysts play a key role as most of the processes beyond the crude unit are catalytic. Since most straight-run fuels produced through fractional distillation do not meet the quality requirements for low-sulfur and higher-octane fuels, most of the crude unit fractions are further processed.
Gasoline with anti-knocking characteristics is made with catalytic cracking of heavy hydrocarbons of selective catalysts and zeolites. Gasoline with low aromatic content (benzene/naphthalenes) comes from alkylation of light olefins with isobutane in the presence of hydrogen and metallic catalysts. The catalytic addition of hydrogen to atmospheric tower fractions results in the removal of Sulfur and Nitrogen and unsaturated compounds (olefins) via the Hydrotreating process. Increases in fuel octane numbers come from catalytic reforming and isomerization processes both of which are also catalytic in nature. Upgrading of heavy hydrocarbon streams through hydrocracking into lighter hydrocarbon molecules is catalytic.
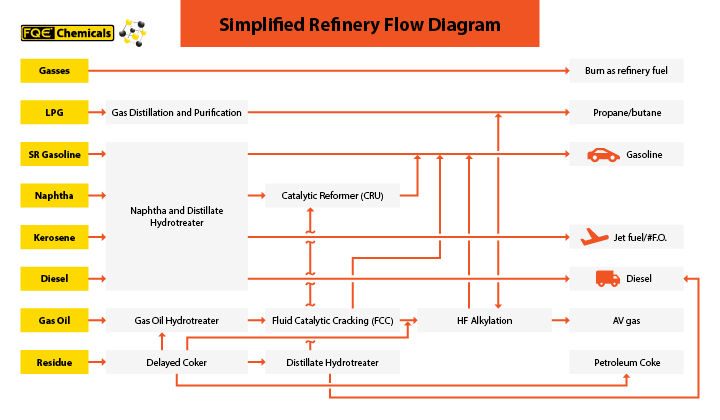
Catalysts promote chemical reactions or accelerate the rate at which a chemical reaction reaches equilibrium. The catalyst provides a surface for reactants to adsorb onto and from which products to desorb from. The role of the catalyst is to lower the activation energy of a reaction by providing a reaction pathway. Heterogeneous catalysis is a surface phenomenon. The reactants must adsorb onto the active surface followed by the desorption of the products from the catalyst surface. Most of the petroleum refining catalysts in a modern refinery contain highly porous catalysts to provide adequate surface area for metals dispersion and the subsequent reaction to occur. The porosity of the catalyst plays a large role in the efficiency of the conversion reaction. It is not surprising that catalysts are sensitive to impurities or poisons that can impact the active surface of the catalyst.
Deactivation of heterogeneous catalysts is a problem that causes the loss of catalytic rate. The deactivation may occur by a variety of mechanisms to include fouling, poisoning, thermal degradation, solid-state reactions, vapor-solid reactions, vapor formation and physical damage to the catalyst structure by crushing.
Methods of Deactivation
There are many mechanisms for catalyst decay. A catalyst solid may be poisoned by any number of a dozen or so contaminants in the feed or encountered in cleaning processes. Its surface, pores and void spaces may be fouled by carbon/coke produced by cracking and condensation reactions. If the catalytic reaction is carried out at high temperatures, thermal degradation may occur in the form of active crystalline growth, collapse of the support structure (alumina) and solid-state reaction of the active phase with the carrier or a catalyst promoter.
There are basically six mechanisms for deactivation of petroleum refining catalysts:
1. Poisoning
2. Fouling
3. Thermal degradation
4. Vapor compound formation
5. Vapor-solid and solid-solid reactions
6. Physical damage to the catalyst support
Poisoning
Poisoning occurs when there is a strong chemical interaction of reactants, products or impurities with the active sites on the catalyst surface. Sulfur poisoning is probably the most prevalent example. An example of reversible poisoning is the deactivation of the acidic sites on catalytic cracking catalysts by nitrogen compounds; either in the feed or introduced through other side processes. This is a reversible problem that is corrected within days after the source of nitrogen is removed. However, most chemical poisons are permanent and irreversibly absorbed to the catalyst active sites. This is the case for sulfur on most metals.
Crude oil contains sulfur and metals such as vanadium and nickel, that act as poisons for many processes. Catalytic reforming and those processes involving petroleum refining catalysts that treat heavier hydrocarbon streams contain higher concentrations of sulfur and metals are more likely found, such as catalytic cracking or hydrocracking.
A chemical poison may act in many ways to deactivate the catalyst. First, a strongly adsorbed atom may physically block multiple reaction sites. Secondly, by virtue of it forming a strong chemical bond, it may electronically modify its nearest neighbor metal atoms modifying their abilities to adsorb or dissociate reactant molecules. Thirdly, it may affect the restructuring of the surface by the strongly adsorbed poison causing changes in the catalytic properties. This is especially true for reactions that are highly sensitive to surface structure. Fourthly, the adsorbed poison blocks access of adsorbed reactants to each other. Lastly, the chemical poison may prevent or slow the surface diffusion of adsorbed reactants.
Tables 1 and 2 below provide a selection of catalyst poisons by structure and catalyst type.
Table 1. Poison by Structure
Chemical Type | Chemical | Reaction |
Group VII & VIA | N, P, As, Sb, O, S, Se, Te | Through s & p orbitals |
Group VIIA | F, Cl, Br, I | Through s & p orbitals |
Heavy Metals | As, Pb, Hg, Bi, Sn, Cd, Co Fe | Occupy d orbitals |
Table 2. Poison by Selective Catalyst
Catalyst Type | Reaction | Poisons |
Silica, Alumina, Zeolite | Cracking | Organic bases, hydrocarbons, heavy metals |
Nickel, Platinum, Palladium | Hydrogenation | S, P, Hg, Zn, As, Pb, NH3, Halides |
Nickel | Steam Reforming | H2S, As |
Nobel Metals | Hydrocracking | NH3, S, Se, Te, P |
Cobalt/Molybdenum Sulfides | Hydrocracking | Asphaltenes, Nitrogen Compounds, Ni, V, Si, As |
The primary effect of low levels of poisons are often the precursor to significant changes in catalyst activity and structure. Poisons may simply lie on the surface of the catalyst and physically block access to the larger inner pore surface or be strongly adsorbed onto the reaction sites and change the physical structure of the surface. Changes in the surface structure are often seen in the changes to activity and selectivity of the catalyst.
The effects of permanent poisons cannot be overstated. Blockages of the porosity, removal of active metal sites and agglomeration of the active metal by poisons often lead to an increase of in the relative rate of coke formation and carbon deposition. This can lead to severe process problems caused by poisoned petroleum refining catalysts.
Heavy Metals
The typical heavy metals encountered in hydrocarbon processing are arsenic, mercury, lead, nickel and cadmium. All are considered to be permanent poisons for precious metal and base catalysts. The heavy metals tend to be absorbed onto the walls of the containment vessel. Arsenic and mercury are particularly bad as they easy alloy with many active metals to form an inactive surface. This effectively reduces the availability of surface area for reactivity.
Vanadium and nickel are well known poisons encountered in catalytic cracking processes. Vanadium is present as an organometallic that is converted to the oxide in the regenerator. The vanadium is then able to migrate to the zeolite catalyst and form a low melting point eutectic with the alumina-silica of the zeolite structure. This leads to permanent destruction of the zeolite and a significant loss of activity.
Nickel deposits on a catalyst surface and can act as a strong dehydrogenation catalyst which then promotes carbon deposition. In FCC units, nickel also promotes unwanted light end gas production. While nickel does not affect activity it does negatively affect catalyst selectivity.
Iron oxide is very reactive with other contaminants like sodium and silicon which then accumulates on the catalyst surface. These accumulations grow and cause pore plugging and reduced catalyst activity.
Organonitrogen compounds act a poison for hydrocracking and catalytic reforming catalysts. These compounds react to form ammonia which then neutralizes the acid functions of the catalyst metal sites.
Water has various negative effects on refinery catalysts. Water can dissolve some soluble components of the catalyst. For example, water will dissolve chlorides from catalytic reforming catalyst thereby reducing the acid site density activity on the surface. This affects the catalysts ability to engage in isomerization reactions. Water enhances aging of the catalyst more so then thermal sintering does. Hydrothermal aging results in crystal growth and permanent loss of activity. Water remaining within a catalyst bed can also cause physical destruction of the catalyst support structure by creation of high pressure steam.
Fouling
Generally fouling covers all phenomena where the surface is covered with a deposit. The best known form of fouling of catalysts is coke formation. Deactivation occurs as a result of carbonaceous residues covering the active sites of the petroleum refining catalysts surfaces thereby decreasing the active surface area. The fouling of zeolite catalyst occurs in the form of coke molecules limiting access of the reactant to the active sites of a catalyst cavity. In short, fouling is a physical deposition of contaminant from the fluid phase onto the catalyst surface which results in the loss of activity due to blockage of reaction sites.
While carbon and coke formation may be the most prevalent type of catalyst foulants, there are others. Dust, tramp iron, inorganic scales from heaters and exchangers, polymers formed from feedstock components, metals present in the feedstock and catalyst particulates (fines) are common foulants that result in a decrease of catalyst activity. These contaminants deposit on the catalyst surface causing pore mouth narrowing and eventual total plugging of the catalyst surface.
Thermal Degradation
Deactivation of catalyst by thermally induced events results in loss of catalytic surface area, loss of support due to support collapse and chemical transformations of the catalytic phase. Crystallite growth and support collapse are known as “sintering”. This occurs at high temperatures exceeding 500°C and are generally accelerated by the presence of water.
The effect of temperature on sintering of metals is understood on the basis of the dissociation and diffusion of surface atoms. As the temperature increases, the surface atom vibration increases. When the Huttig temperature is reached, less strongly bound surface atoms dissociate and diffuse across the surface. When the Tamman temperature is reached, the atoms through the bulk catalyst move about freely. This movement can either increase surface activity or moderate it due to uneven crystallite size and growth.
So what does this all mean? Petroleum refining catalysts are expensive materials and are protected by refinery staff to ensure long reactivity life. Controlling the impurities present in the feedstock crude oil streams being processed, controlling operational conditions, minimizing in-process contamination sources and insuring that processing aides and cleaning processes and products do not cause undue presence of catalyst poisons is essential.
At FQE Chemicals, we deliberately and meticulously create products that avoid the use of any known or suspected chemical catalyst poisons. You can feel certain that products from FQE Chemicals will not negatively impact your catalyst performance. If you have questions or have concerns about this topic, contact your FQE Chemicals representative for answers.