Part 9
Many of the process streams in a refinery contain unsaturated hydrocarbons, sulfur compounds, nitrogen compounds and other materials (metals) that interfere with some of the refining processes. Hydrotreater fouling must be dealt with to ensure the unit operates effectively to protect units further down in the refinery process.
Hydrotreating is a catalytic process that makes use of by-product hydrogen from the catalytic reforming process, to saturate hydrocarbons (change a carbon-to carbon double bond to a carbon-to carbon single bond) by adding a hydrogen atom to each of the two carbon atoms.
In doing so, the process removes sulfur, nitrogen and metals from a wide variety of process streams. In general, each of the major streams coming off the atmospheric tower will have a hydrotreating unit.
Hydrotreating is essential in the preparation of feedstocks for many downstream processing units. The catalytic reformer unit catalyst can be poisoned by sulfur in the feedstock. Without desulfurization, the catalyst’s life would be greatly reduced. Therefore, hydrotreater fouling must be dealt with to ensure the unit is performing effectively and protecting the units downstream. Catalytic cracking also benefits from hydrotreating. Sulfur plates on the catalyst and results in shorter run times between regeneration and more sulfur dioxide released to the atmosphere during regeneration.
Hydrotreating improves the burning characteristics of distillate fuels. These fuels contain a high percentage of aromatic compounds which create a lot of smoke when they burn. These fuels are said to have a low “smoke point”. By saturating the aromatic compounds, the smoke point can be raised resulting in a cleaner burning fuel and reduced pollution.
Process Description
There are many specific hydrotreating processes. The processes differ mainly in the type of feed that is to be treated. Many of the refinery processes benefit by having their feed stream pretreated by the hydrotreating process; therefore, a number of the petroleum streams in a refinery will undergo hydrotreating. While the processes are essentially the same, the synonyms for the hydrotreating process are:
- Hydrofining
- Unifining
- Hydrosulfurizing
- GO-fining (treating gas oils)
- Residfining (treating of residuum)
- Remove sulfur and ammonia
- Reduce the metal content of the oil
- Saturate carbon-to-carbon double bonds
Figure 1 is a flow diagram for a British Petroleum hydrofiner design which is typical of most hydrotreating processes to desulfurize, hydrogenate and improve the general quality of a wide variety of hydrocarbon streams from gas through waxes.
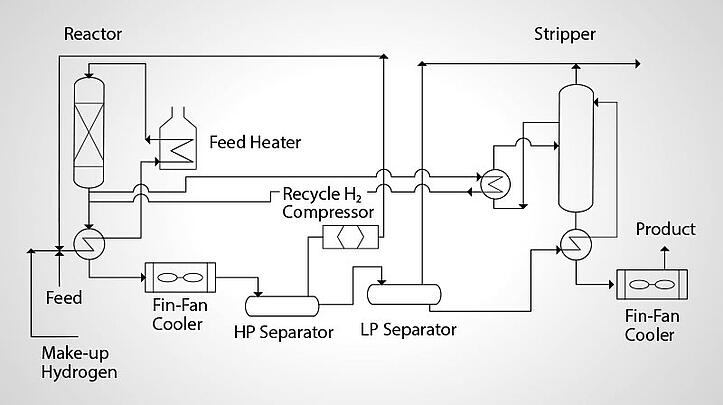
Hydrofiner
The feedstock is mixed with an excess amount of hydrogen-rich gas and preheated by cross-heat exchange with the reactor effluent and in a direct-fired furnace before entering the reactor. In the reactor, the hydrocarbon/hydrogen mixture is passed over a fixed-bed catalyst which is a mixture of cobalt and molybdenum oxides. The catalyst promotes the reaction whereby hydrocarbons are saturated with hydrogen atoms and sulfur and nitrogen in the hydrocarbon are replaced by hydrogen.
The reactor effluent is then cooled and enters a high pressure separator, where excess hydrogen is removed from the oil. The excess hydrogen is compressed and recycled back into the feed stream. Hydrocarbon is drawn off of the bottom of the high pressure separator and charged to a low pressure separator. In the low pressure separator, most of the gases (H2S, ammonia and some hydrogen) remaining in the oil are flashed off. The remaining oil is heated and pumped to a stripper tower.
In the stripper tower, the remaining hydrogen sulfide, ammonia and some light ends are steam stripped from the hydrocarbon and removed via an overhead condenser. The product is drawn from the tower bottom, cooled and sent to storage or other refinery processes. A fractionator, mat must also be included in the process flow if product separation is desired.
The catalyst bed will require periodic regeneration. This is done with the bed in place, in the reactor, by steam/air decoking. The useful life of the catalyst can be two years or more.
Types of Hydrotreater Fouling
The feed preheat bundles will become fouled with salts (primarily ammonium chloride) and substantial amounts of iron sulfide. These bundles can almost always be chemically cleaned to remove hydrotreater foulingf with an alkaline detergent followed by a sulfide scale remover. Often an emulsion-type product containing an iron sulfide scale remover can also be effective.
The preheat furnace is susceptible to the same type of fouling as the preheat bundles. However, in addition to salts and iron sulfide, there is the possibility of coke and iron disulfide deposits. Both of these types of deposits are insoluble in most chemical solvent systems. In most cases, if the furnace is coming down, so is the reactor and the catalyst in the reactor will be regenerated. The furnace will be used as a heat source during catalyst regeneration and this will remove any coke deposits that may be present. The steam/air decoking process that is used to regenerate the catalyst will also oxidize the insoluble disulfides to soluble sulfates. The furnace will also have fuel lines that will become plugged and may require periodic cleaning. These fuel line deposits are mainly organic that can be removed chemically. If stripped gas is used as a fuel, there will likely be an iron sulfides deposit present in addition to the organic matter.
The fouling that is found in the steam stripper will be mainly iron sulfide with some organic material. The overhead condenser and accumulator are susceptible to severe corrosion from water/H2S mixtures; therefore, the structural integrity of these units should be checked before making an attempt to clean them.
Both fin-fan coolers and water-cooled heat exchangers are found in hydrotreaters. The air side of the finfan coolers will become fouled with airborne debris that can be removed by washing with an appropriate chemical product. The water side of the water cooled exchangers will become fouled with iron oxide and hard water deposits. These hydrotreater fouling materials are easily removed with a well-chosen chemical cleaning product. Typically, acid-based or chelant-based solvents are used for this purpose.
The reactor will become fouled with coke and heavier metals. The coke will be nearly impossible to dissolve in a solvent. However, these materials will be removed during catalyst regeneration, so it is unlikely that the reactor will require cleaning.
Cleaning of Hydrotreater Fouling
The heat exchange efficiency of the preheat bundles determines how hard the direct-fired furnace has to be fired to bring the feed up to the proper temperature. These bundles are also used to cool the reactor effluent. Their efficiency will also affect the separation of the recycled hydrogen from the oil flow. These heat exchangers will require periodic cleaning to maintain an efficient rate of heat transfer and occasionally a cleaning is required because of excessive pressure drop across the exchanger.
Heat exchange equipment is best cleaned by the fill and circulate chemical cleaning method. While the relatively small volume of chemicals required to clean most exchangers will not justify a chemical cleaning process, a chemical process will be the most effective and time efficient method. Purging the exchangers of gases and hydrogen sulfide can be quickly accomplished through chemical cleaning techniques.
Furnace tube fouling can result in increased fuel consumption due to a higher firing rate and coking of organic matter in the deposit. Furnace tube deposits may also slough off and plug the catalyst bed in the reactor. If a large portion of the deposit is inorganic, the furnace tube may still require cleaning even if the furnace is used during catalyst regeneration. A fill and circulate chemical cleaning technique is the best and the easiest method to clean fouled furnace tubes and water blasting will likely be required to remove coke deposits.
The hydrogen recycle system is likely to be the most system most effected by heavily hydrotreater fouling. Cleaning of this system is necessary because the scale can be carried over into the reactor where it can interfere with catalyst performance. The method used to clean piping systems (hydrogen recycle lines, steam lines, lube oil systems etc.) will be determined by the type of material that is to be removed. Lube oil and seal systems would probably be cleaned as a hydraulic system circulating with a sublaminar flushing unit.
Systems that would require extensive temporary piping to form circulation loops are good candidates for vapor-phase cleaning or possibly foam cleaning processes. When a mixed organic and inorganic deposit is to be removed during a chemical cleaning, the use of an emulsion-based product should be considered. The use of emulsions can reduce the amount of time required for chemical cleaning and the volume of waste that must be disposed of.
The steam stripper and the associated condensers and accumulators will require chemical cleaning to remove corrosion products, heavy organics and sludge that will interfere with the steam stripping process and may reduce product quality.
As hydrogenation is an exothermic reaction, the hot reaction products must be cooled to permit the efficient removal of excess hydrogen from the product. This cooling is accomplished with water-cooled heat exchangers and fin-fan coolers. Since make-up hydrogen is of the major costs associated with this unit, the process coolers will need to be chemically cleaned to maintain their efficiency.
Various chemicals are recommended for chemical cleaning of these many system components. It is important to evaluate the vendor’s knowledge of application and the choice of chemical products to insure that cleaning operations are effective and efficient to clean hydrotreater fouling. Developments in chemistry have resulted in more effective chemical products for removing foulants. Do not be lured into believing that inexpensive commodity products are all that is required. New products offered in the industry have dramatically improved cleaning results and, as importantly, reduced the outage times required.