Part 3
Part 3, focusing on preheat train decontamination, in the series on how the chemical industry is solving challenges in the industrial sector.
In the previous article, we spoke about the operation and cleaning of the Desalter drum. Upon leaving the Desalter, crude oil will go to the Atmospheric Tower where the first actual separations will take place through boiling point differential distillation. This is where preheat train decontamination may become important. To accomplish the fractional distillation, the crude oil feed charge will go through preheat bundles on the shell-side, generally, where it will pick-up heat from already processed streams from the Atmospheric Tower.
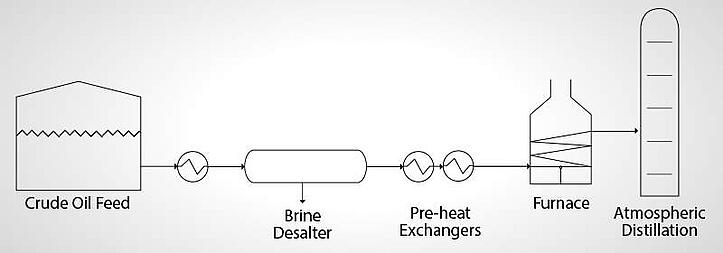
Preheat Train Fouling
Along with the furnace, these exchangers are the most susceptible to fouling in the refinery so multiple spares are typically found per bundle. When the crude oil preheat bundles and furnace become fouled, it results in higher fuel consumption costs to heat the crude oil and reduced capacity.
In these heat exchangers fouling deposits are formed during the heating process. The heat exchangers will heat the crude feed to around 204°C (400°F). While the deposits are hard and black, the operating temperature is not hot enough to form “coke” – pure carbon. This foulant is not coke even if it is often referred to as coke.
The exchanger fouling is typically a mixture of iron, silica and organics. It can be up to 50% inorganic in composition. The organic portion of the deposit is high molecular weight asphaltenes, waxes and some linear and branched polymers.
Preheat Train Decontamination
The method used for cleaning these fouled crude preheat bundles is often high pressure hydroblasting or a fill and soak chemical cleaning using strong oxidizing agents such as potassium permanganate. But do not believe that these two measures are the only effective processes in which to clean.
While this fouling is difficult to chemically clean, the bundles can be cleaned in-place if you select the appropriate chemicals to do so. To effectively clean these bundles chemically, solvating the organic portion of the deposit allows for removal of the binding compounds. This is the most difficult and critical part of the cleaning process. Up on removal of the organics, the loose inorganic debris can be flushed-out hydraulically. Or, if desired, the inorganic scales can be chemically dissolved by the selection of ligand-forming chemical products or via an inhibited acid wash.
On exiting the preheat exchangers the crude will go to a direct fired furnace to be heated to 371°C (700°F) or more and then go to the atmospheric distillation tower. The same type of fouling deposits are found in the furnace as are found in the preheat exchangers. However, many refiners “decoke” these furnaces in-house. The process involves burning off the deposits by passing a mixture of steam and air through the furnace tubes. This does not mean that this process is very successful.
Chemical cleaning of the furnace can be accomplished by the same chemical products that are employed with cleaning the preheat exchangers. Next time consider chemical cleaning the preheat train using effective, state-of-the-art chemical products. You will save outage time and reduce your waste generation.