Applications
Heat Exchanger Cleaning
With chemical heat exchanger cleaning there is no pulling equipment out of service for a week, no hydroblasting, no re-fabricating of bundles, no damage due to excess handling and reduced manpower requirements.
The heat exchange procedure is one of the most important processes in modern plants
Whether in oil refining, power generation, chemical production, paper manufacture or waste treatment; the transfer of heat is vital to efficient operation. During normal operation, heat transfer surfaces will foul and heat transfer and production rates will decline. It is imperative that these fouled surfaces be returned to cleaned condition so efficient production can continue.
Our chemistries have been blended to be effective in refining hydrocarbons, water-based scales, high LEL materials, and other foulants found in the industry.
Video Description
Sample provided by petrochemical facility located in Baytown, Texas.
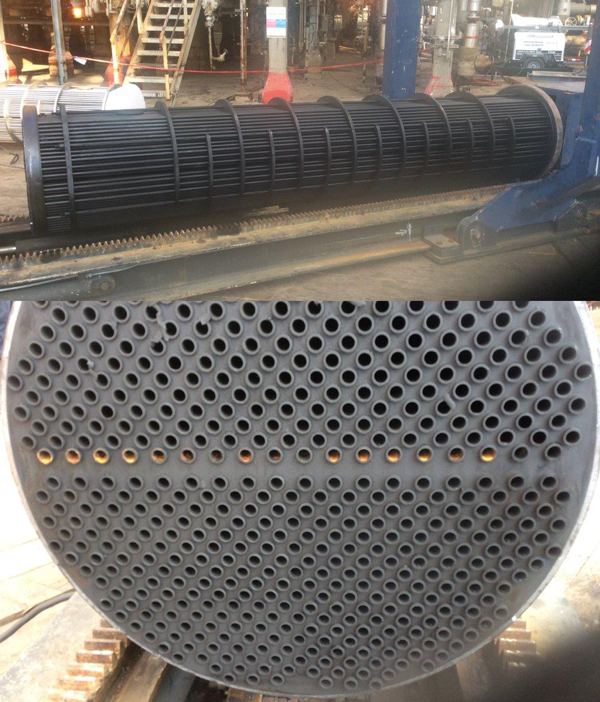
Clean Exchangers following Treatment
Heat exchanger cleaning without pulling them for maximum speed and savings.
Pulling a heat exchanger for cleaning is frustrating, time-consuming and expensive, but we can help. We custom engineer solutions and processes that clean heat exchangers in place, without the delay, frustration, and expense. No pulling equipment out of service for a week. No hydroblasting. No re-fabricating of bundles due to excess handling.
Forget separating the bundle from the shell or having to replace numerous parts for a week-long replacement process. Our chemical heat exchanger cleaning method lets you clean heat exchangers without pulling them, returning your equipment to premium condition while improving your schedule, safety, and bottom line.
The process is simple: after you isolate the selected unit or bank of units, we circulate a solution of carefully selected and blended cleaning chemicals. One of our experts administers the process and monitors it until completion.
Advantages
1
In-place cleaning
2
Minimal waste is generated
3
Less manpower required
4
Completely recoverable oils for hydrocarbon based foulants
5
Greatly reduced maintenance expense
6
Less handling of expensive pieces of equipment
The Results
1
Less exposure to safety risk
2
Lower project costs
3
Faster project execution
4
Improved future heat transfer
Reduce downtime and elevate profit with chemical heat exchanger cleaning
Once customers use our proprietary chemistry to remove foulants without having to pull the unit, they rarely revert to their traditional way of doing things. The economics of our chemical-based processes are just too compelling.
Expedite heat exchanger cleaning
Our process takes about one third as long as a conventional mechanical cleaning. Fewer interactions are required, demanding less human resource burden and more peace of mind when every turnaround and outage hour counts.
Minimize risk to equipment and personnel
The process is totally self-contained. There’s no risk to personnel and no need to move or modify the heat exchanger for cleaning (incurring risk to the unit). Our formulations are compatible with almost all metals to include stainless steels, carbon steels and most soft metals.
Improve equipment performance
After we’ve applied the chemical treatment, you’ll find that it takes longer for your heat exchanger to foul next time. Heat transfer numbers will go through the roof and stay there with longer potential run times than ever before. Overall heat transfer coefficients return to design values. Pressure drop values decrease allowing for more product throughout.
Marginalize disposal costs
Waste disposal is minimized. If hydrocarbons are the foulant then they can be re-run in refining processes or blended into the fuels market. If the foulant is water based, our chemicals are designed to be compatible with current waste treatment systems.
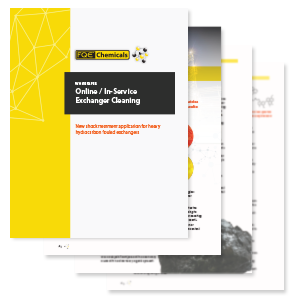