Refinery
Chemical Cleaning Solutions for Fouled Hydrocracker Units
Exposure to catalytic cracking assists in separating light gas oils into smaller gasoline range molecules. A fouled hydrocracker unit can cause several issues, including product quality.Â
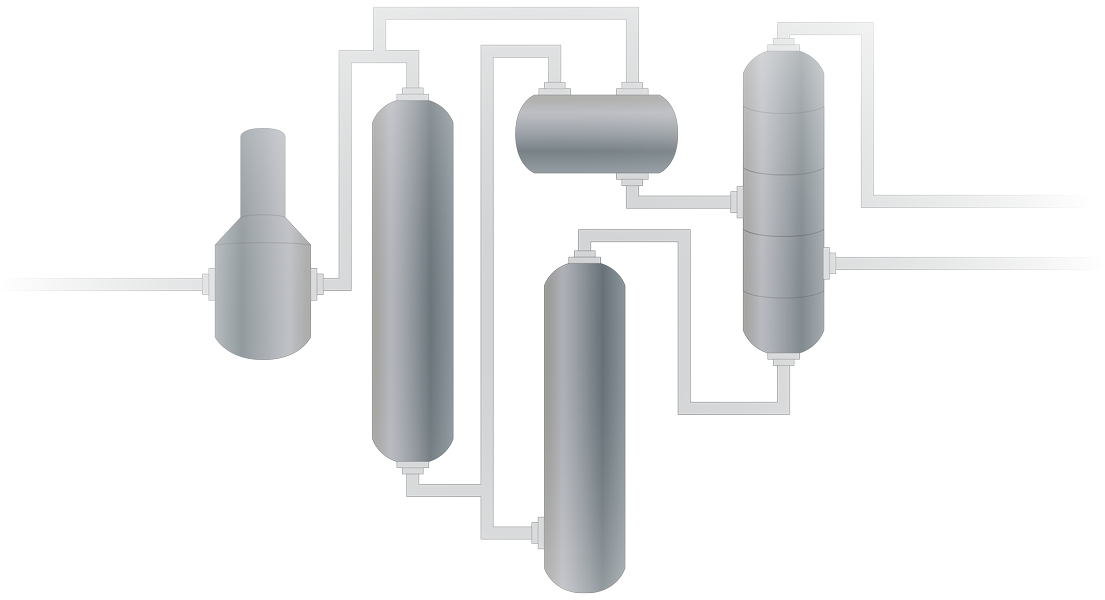
Chemicals Utilized
Hydrocracker Process
Like the fluidized catalytic cracking unit, the hydrocracker has stages that the product goes through before it is further refined into final products.
1
To begin with, the feed is heated. And, hydrogen is added to enable the product to properly react with the catalyst.Â
2
Then, the feed enters the reactor at the top and the product encounters the catalyst. The cracking begins and the creation of olefin molecules occurs. Finally, the olefins combine with the hydrogen molecules to create iso-paraffins.
3
Next, the fin-fan coolers and exchangers cool the product. And, it continues to an H2 separator to remove hydrogen. Next, a low-pressure separator flashes off the light hydrocarbons.
4
Finally, the bottom products continue to a fractionator tower where products are separated into a range, including naphtha and gas oils. The lighter hydrocarbons go into a splitter to separate gasoline range materials.
What Problems do the Hydrocracker Cause?
During the multiphase process, the hydrocracker components can become fouled. The fouling creates issues with product quality and the ability to effectively crack molecules.
Pre-heat exchangers can foul with heavy oils and varnish. Similarly, fin-fan coolers and water-cooled exchangers foul with oil. Additionally, these components can also have a water-born scale build-up.
Not only does the fractionator tower and associated equipment columns have oils and light end vapors affecting their performance, but also the bottom can have heavy polymer products. This is due to the olefin polymerization.
Each of the separators contains LEL vapors and oils from the process that are typical contaminants within the refinery.
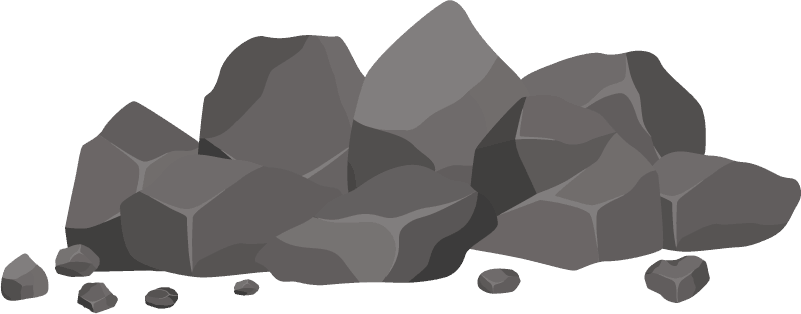
Our Chemical Cleaning Solution
The fouled hydrocracker unit can remove the contaminants inhibiting the performance of the unit through chemical cleaning. Equally important, the resulting suspended foulants can be recovered in the refinery process. Which both increases revenue and decreases hazardous waste disposal.
1
Dissolve Heavy Organics
First, to address the heavy organics within the pre-heat exchangers and separators, FQE® Solvent-H+ can be circulated. Of course, the organics dissolve and remain suspended in solution.
2
Degrease Fin-Fan Coolers
Next, is the chemical cleaning of the oils in the fin-fan coolers. This is achieved through utilizing FQE Fin-Fan Degreaser.
3
Descale Exchangers
At the same time, the water-cooled exchangers will use FQE Scale-Solv to remove the water-born scale contaminants.
4
Decontaminate Gases
Last, the degassing of the separators, fractionator and other associated separator equipment may begin. By using FQE LEL-Vapor the equipment is decontaminated of the harmful LEL vapors present.