Applications
Degassing
Our chemical degassing products will help you gain a competitive edge, increase profitability, and reduce turnaround time for your operation.
Vapor Phase Cleaning: Shortening the Race to Inspection
For decades refiners and chemical plant operators have been faced with the need to remove hazardous and flammable gases from their process equipment prior to personnel entry or beginning any maintenance or inspection activities. Vapor phase clearing of equipment or vessels has been the traditional way degassing was done, tons of steam was used to remove these contaminants from the process units. This steaming out took time, resources, and produced copious condensate that had to be treated in wastewater treatment.
In recent years plant operators have realized that using chemical degassing products with steam or as a cascade application will help them gain a competitive edge, increase profitability, and reduce turnaround time for their operation.
Utilizing vapor-phase cleaning and patented LEL-Surface, this process effectively eliminates entrapped hydrocarbons within pores of the metallurgy. It empowers the steam droplets which navigate complex unit geometry, condensing and cleaning and clearing the system at the same time. By injecting steam through existing inlets with LEL-Surface, a visual endpoint is reached when the water runs clear, indicating where to stop and proceed according to the schedule saving time.
The enhanced cleaning power results of LEL-Surface provides a shortened operation time, saving a significant amount of water. This reduction in water usage translates to less post-job processing and reduced wastewater. The condensate can go to the API separator via the oily water sewer and the skimmed oil may be directed to a slop tank, reclaiming unrealized hydrocarbons as profits rather than waste.
Steam, exhibiting a propensity to take the path of least resistance, would prove ineffectual on its own, much like water forming beads on a freshly waxed car, never truly making contact. In contrast, LEL-Surface, unlike water-based alkaline soap that may leave stress-cracking sodium ions, employs advanced technology and reagents to dissolve and break down contaminants, resulting in the acquisition of a US patent. Proper dissolution and draining ensures that the oil phase becomes mobile, facilitating more extensive flow throughout blockages.
The inherently cleaner system is safer, with reduced residual build-up. Confined space manned entry becomes more straightforward, eliminating the need for high-pressure hydroblasters and minimizing water usage, solid waste, and TCLIPS for waste handling landfill requirements. The simplified entry allows easier identification of problematic areas requiring attention and workover.
Maintenance can independently perform the procedure, eliminating the need for third-party contractors and saving time. The absence of waiting for contractors results in quicker completion, potentially avoiding night shifts or overtime. This approach removes the need for roll-off boxes, permits, gate passes, and additional contractor equipment.
Upon achieving an effectively cleaner system using LEL-Surface, any pyrophoric iron sulfide can be pacified with the FQE Pyrophoric product in situ, reducing risks associated with ignition.
Applications
Caustic Treaters
Crude Units
Ethylene Units
Flare Systems
Gas Compressor Systems
Hydrocarbon Tanks
Hydrofiners
Hydrotreaters
Merox Units
Natural Gas Sweetening Units
Pipelines
Pipestill
Reformers
Sour Water Tanks
Sponge Absorbers
Ethylene plant oil and water quench systems
Solvent recovery systems in polymer production
Any system containing light ends
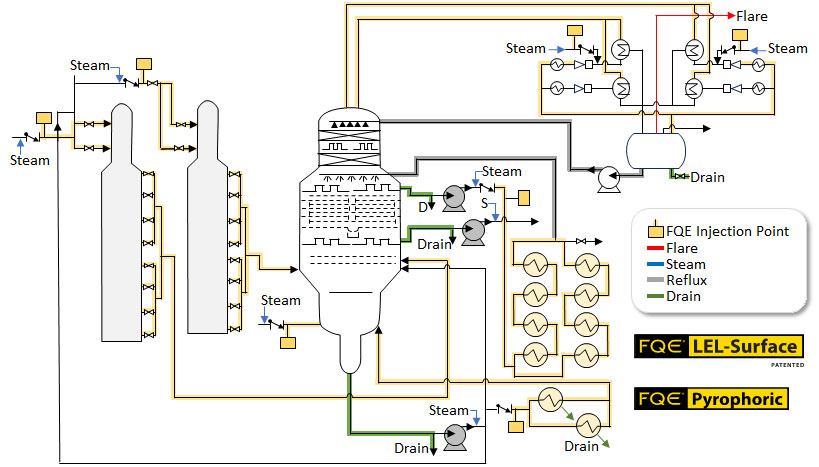
Degassing by Unlocking the Power of Water
LEL-Vapor activates water to capture VOCs and LELs of noxious gases as degassing time is substantially reduced. Applicable for all light hydrocarbons such as benzene, gasoline, alkylate, styrene, and xylene (BTEX). Reduces the need for thermal oxidizer (TO) or internal combustion engines, which lowers costs. Can be used when venting/flaring is not available or feasible. Our chemical degassing products will help you gain a competitive edge, increase profitability, and reduce turnaround time for your operation.
LEL-Vapor is ideal for degassing tanks, vessels, and units quickly. Especially where using a TO is cost prohibitive or to reduce the amount of TO time to reduce the incurred costs. Using LEL-Vapor with water can reduce days, even weeks in degassing time as compared to the fill-drain technique where a tank is filled with a cutter oil (i.e. diesel) and then drained in hopes of extracting the light ends high vapor pressure VOC/LEL producing material in the tank heel. This process proves to be time consuming, rather ineffective, and highly variable as repetitive nature can be unpredictable. It’s not uncommon to repeat the fill and drain process more than a half dozen times and take weeks, rather than using water and LEL-Vapor and be done in 1-day. This allows the turnaround to happen faster and more systematically as the degassing step is a single stage and predictable.
Superior degassing with FQE® LEL-Vapor
The demand for system decontamination, including degassing, which meets or exceeds constantly changing regulatory safety and environmental requirements is growing. LEL-Vapor is a safe, non-hazardous, non-petroleum-based product for use in plant process equipment decontamination and degassing. LEL-Vapor is added to water in small fractional amounts to be applied either as part of a liquid cascade, water cannon, or fill procedure.
Can be merged into the shutdown phase, daily cleaning, or spill response to minimize turnaround time. Degassing with LEL-Vapor reduces personnel safety concerns and reduces the release of harmful gases into the environment.
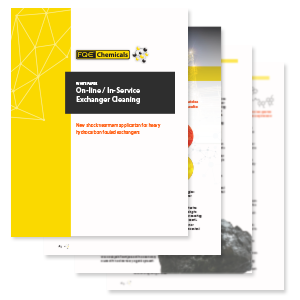
White Paper
Online/In-Service
Exchanger Cleaning
Learn about a new shock treatment application for heavy hydrocarbon fouled exchangers.
Wastewater Disposal
Both FQE LEL-Vapor and FQE LEL-Surface will not strongly emulsify residual oils, allowing for a rapid phase separation of the oil phase from the water after the circulation fluid has been removed from the unit. The residual oil floating on the surface can be recovered and reprocessed for profit or disposed of. The remaining wastewater will be relatively free of oils and can be sent directly to the wastewater plant for processing. No prolonged delays in wastewater processing are expected.
The FQE products have been designed with wastewater disposal concerns for bioculture toxicity and COD.