Applications
Chemical Decontamination
Eliminate dangerous elements inside your equipment in a way that minimizes both cost and safety risk with our chemical decontamination strategies.
Make your equipment safe to enter without risking safety or downtime with chemical decontamination
Our advanced chemical decontamination processes render the inside of your equipment completely safe for hot work, eliminating potentially dangerous solids, residual oils, and gases without sacrificing your tight outage schedule.
Hydroblasting solids. Managing dangerous LEL’s. Sweating turnaround hours. Creating a totally safe work environment within your equipment can be a trying experience—one which not only creates safety challenges for your team but also threatens to delay turnaround plans if workflows don’t come together as planned. And when it comes to the cleaning phase of maintenance turnarounds, failure to achieve a suitable environment quickly and predictably can cause costly and frustrating bottlenecks.
Decontaminated Bubble Cap Trays
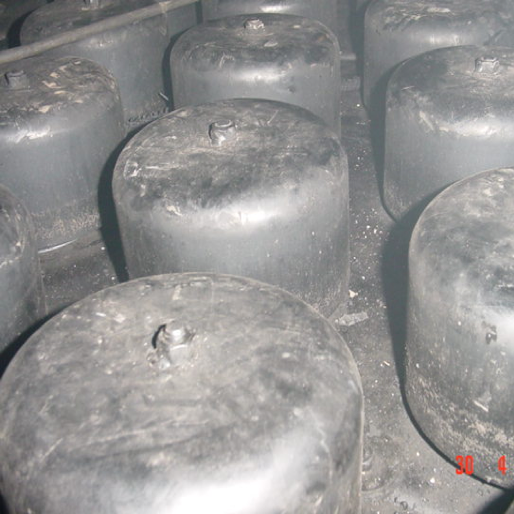
The Solution
FQE® Chemicals high-performance chemical cleaning processes eliminate dangerous elements inside your equipment in a way that minimizes both cost and safety risk. Using a solution custom engineered for your equipment and its operating dynamics, we can introduce a series of chemicals into your equipment that make it safe for hot work both quickly and reliably and keep the equipment self-contained in a closed-loop system. You’ll get:
1
Less exposure to safety risk by letting the chemistry perform all of the work previously done mechanically
2
Lower risk to project costs with a predictable, reliable resource (our chemicals get the job done in a predictable time period with no surprises)
3
Faster project execution to make the most of outage and turnaround downtime
Decontaminated Bubble Cap Trays
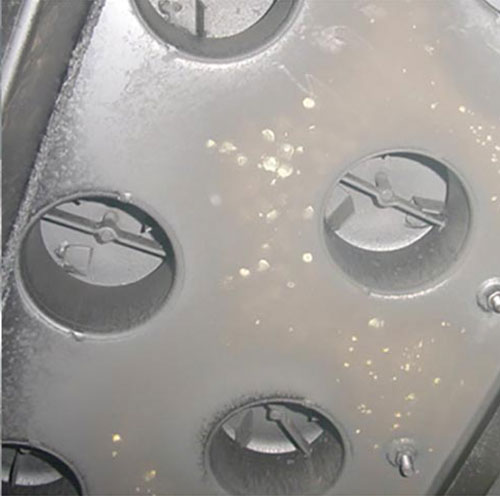
Decontaminated Demisters Trays
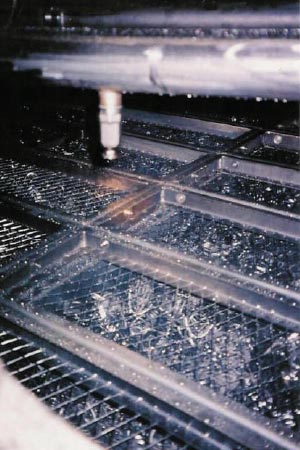
Leverage our expertise in chemistry
Our clients leverage our expertise in chemistry and facility engineering to slash maintenance, operating, and environmental costs through the creation of solutions that optimize the way your plant works. Through chemically-based decontamination, degassing, and polishing technologies and techniques, you can reliably clean any critical process equipment including:
Heat exchangers
Associated piping
Reboilers
Distillation towers
Less human contact, less safety risk
Our chemical decontamination processes let the chemistry take the lead, reducing human touch points with the equipment during the cleaning process. Human exposure to dangerous substances and situations is minimized. These seemingly small situations whereby chemical processes can take the place of actual people add up to significant improvements in both safety prevention measures, manpower utilization, and overall plant economics.
Molecules don’t take a lunch
You can’t afford to employ anything but the most certain resources to execute your next pre-maintenance equipment cleaning. That’s why so many asset managers trust our chemical decontamination process. By working with the design of their operating environments, we enable our customers to make the most of available resources: using chemical solutions that work 24 hours a day when they’re needed most. With minimal equipment and minimal human resources, your equipment gets permitted for hot work quickly, easily, and dependably