Part 15
Foam Cleaning Technique
In the previous article we discussed the concept and use of foams as an effective cleaning methodology. Part two is about chemical solvents, inhibitors, foaming agents and other aspects of the foam cleaning technique.
Foam Cleaning Technique: Solvents
Foam can be used in many applications to apply a variety of chemical products for cleaning of systems. However, the most prevalent chemicals used for effective foam cleaning techniques are acids and alkaline liquids. Though most acids and alkaline cleaning liquids can be foamed, hydrochloric and sulfuric acids are used the most. Inhibited hydrochloric acid can be foamed for use on all metals except stainless steel and aluminum. These two exceptions are, however, effectively cleaned with foamed sulfuric acid with an acid intensifier added. For removing scales that contain silicates, a properly selected acid intensifier additive in combination with hydrochloric acid is very effective.
While acids and alkaline products are the most often used for foaming applications, other chemical products that are typically not thought of as “foamable” can and are indeed used successfully in foaming applications. Amongst these materials includes alcohols, glycol ethers and some hydrocarbon solvents. Typically, these materials would be precluded from use in foams as they have high vapor pressures that can collapse generated foams. However, the advancement of surfactant technology provides us with materials that can create a variety of foam types that can support these solvent types. This is advantageous for cleaning difficult, heavy deposits of organic debris that alkalinity alone is not adequate.
Of interest is foaming applications for voiding compartments of high LEL producing constituents such as hydrocarbon vapors. When it is impractical to use vapor-phase steam induction for voiding spaces of LEL vapors, another effective method is the application of high surface area foams containing the appropriate degassing agent. Please note that not all industry degassing materials can be applied through a foam-in method due to inadequate performance characteristics of the “degassing’ product. If the correct degassing agent is selected, foaming of the absorptive chemicals both relieve high LEL levels and remove latent organic deposits within equipment at ambient temperatures without steam pressure.
Foam Cleaning Technique Inhibitors
Foamed hydrochloric and sulfuric acid is satisfactorily inhibited with a various industry available acid inhibitors.
For hydrochloric acid, one gallon of inhibitor per 1000 gallons of solvent when cleaning at temperatures of 175˚F or below and using acid concentrations of 7.5% or less is often sufficient. For inhibiting stronger acid solutions, two gallons per 1000 gallons of acid solvent solution is required. When cleaning equipment that contains cast iron, two gallons of inhibitor per 1000 gallons of solvent is recommended in acid concentrations of 10% or less with a maximum treating temperature of 120˚F. Three gallons if the acid concentration is over 10% when cleaning cast iron. Under no circumstances should the temperature of the treatment exceed 200˚F on any metal surface. At treatment temperatures of 176-190˚F, the use of two gallons per 1000 gallons of solvent at concentrations of 7.5% or less; and three gallons of inhibitor per 1000 gallons of solvent in acid concentration over 7.5% are recommended.
Exceptions for these treatment temperatures include bimetallic junctions, stressed metal or welded metals and tube ends. When such metals are present, treatment temperatures should not exceed 175˚F.
For sulfuric acid, two gallons of inhibitor per 1000 gallons of solvent when cleaning at 150˚F or less and using acid concentrations of 2% or less is adequate.
Agents for Effective Foam Cleaning Technique
For the most effective foam cleaning techniques, the agent used is important. The quality of the foam is determined by the composition of the surfactant mixture used to generate the foam. Solvents can be converted to a suitably stable foam after the addition of a properly selected surfactant or foaming agent.
Many different types of foam characteristics can be created from high foam volume with short half-lives to low, dense foam volume with high persistency. Ideally, you want a foaming agent mixture that has a low freezing point, preferably below -20˚F and upon heating will again foam at +20˚F. Under these conditions, no phase separation will be observed and has a wide range of operating temperatures of 20˚F to, at least, 150˚F.
Achieving the various foam characteristics that are defined for the cleaning operation requires blending of surfactants that will meet the design parameters. Among the various surfactant products that are considered as foaming agents are betaines, amine oxides, alkyoxylated phenols, long-chain amides and others. Those skilled in the art blend mixtures of these and other suitable surfactants to achieve the desired foam quality for application.
In application, the selected foaming agent is typically added at concentrations of approximately 1-1.5%, by volume, to the cleaning solvent mixture. In some instances, higher concentrations of 2-3% may be required if there are materials present that can act as defoaming agents, such as glycols. After addition of the foaming agent, a continuous circulation of the cleaning solution should be maintained for a minimum of 30 minutes before foam generation is initiated.
Equipment
Equipment used in effective foam cleaning techniques consists of a solvent mixing tank, metering units and a foam generator. Any conventional tank can be used as the solvent mixing vessel. A foam generator consists of aerators and a separator tank. A drawing of a general foam generator is provided below.
Foam Generator
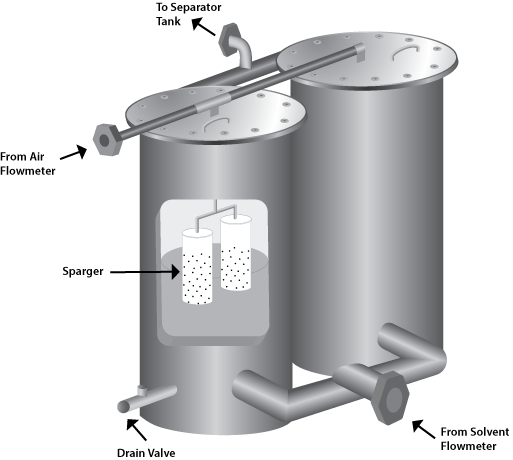
The principle of operation is simple. The metered solvent flows upwards through the aerators, while air, introduced from the top, partially converts the liquid to foam. The resultant mixture of liquid and foam passes through the separator where the liquid trapped in the separator is recycled to the solvent flowmeter. With proper control of the cycling rate, a constant liquid level can be maintained in the separator while continuously generating foam. The separator tank should be sized so that the effluent foam has a conversion ratio of approximately 15:1 when the generation rate is at its maximum of about 1000-1200 gpm. The generator should be pressure code for at least 40 psi with a safety valve.
The client must be able to supply air at the rate of 100 ft3 per minute and under a pressure of at least 20 psi for a foam generation rate of 600 gpm. For foam generation rates of up to 1200 gpm, an air supply of 365 ft3 per minute at 20 psi minimum are required.
In application, if the equipment to be foam cleaned is larger than the capacity of the foam generator, then the equipment must be cleaned in sections or it can be cleaned all at once using more than one generator.
Miscellaneous Comments
Foam cleaning technique is important to achieve successful results. The stability of the foam and the foam volume will decrease as the foaming process proceeds. This is due to the liquid phase of the foam taking in the contaminant. Early in the process, the effluent foam and liquid may appear dirty and of poor quality. As the foaming treatment continues the effluent foam quality will improve. Past experience has proven that it is not advisable to reuse any of the cleaning solvent that drains from the foam and collects. Frequently, used solvent has high concentrations of contaminant that will prevent it from foaming properly and recontamination of the system may occur.
Closing
Foaming is another methodology to consider when liquid-fill, cascade circulation or steam induction methods are not feasible or practical. Foam cleaning techniques work well if they are designed with the proper equipment and chemicals. Another tool for your tool box.