Part 8
The Crude Unit – Vacuum Tower Decontamination
Upon leaving the desalter, the crude oil will go to a crude processing unit where the first actual separations will take place. The feed charge will pass through the preheat bundles, generally on the shellside, where it will pick-up heat from an already processed stream. These bundles are where one type of refinery coke is formed. This is where vacuum tower decontamination needs to occur. The temperatures are not high enough to form true carbon, but the deposit will still be extremely hard to remove chemically.
In previous discussions we have discussed this problem and also identified that technology has advanced so that very effective chemical cleaning of these “coke” (asphaltene) deposits can be successfully accomplished in-place while off-line.
Quite frankly, better outcomes are possible if operations would chemically clean these exchangers more often and not wait until the exchangers are nearly plugged solid.
With in-place cleaning now very effective and with a short term duration, chemical cleaning for vacuum tower decontamination should be more the norm.
The crude will next go through a fired furnace to be heated to 371°C (700°F) or so and will then go to the atmospheric distillation tower. Here it is broken down into four major fractions. Each of these fractions will be further processed to water as in the gas stream or to further purify the individual streams. Often additional towers are used for the extra treating with the bottoms being recycled back to the atmospheric tower.
Should heavy end processing be required, and this is the most likely condition given the increasing nature of the incoming crude being sour and lower API gravity, the atmospheric tower bottoms will be charged to a vacuum distillation tower where low pressures are used to separate any lighter end materials which may be present. On its way to the vacuum tower, the feed will go through another fired furnace to raise the temperature to 399 – 427°C (750 – 800°F). The vacuum distillation tower operates at an internal pressure of approximately 5 psia. As the residuum enters the tower, the lighter fractions begin to boil and flash and rise through the column. Lubricating oils are separated from the residuum and condensed in the column using reflux streams.
Since flashing is a cooling process, superheated steam is introduced into the vacuum tower to maintain the temperature. The products from the vacuum tower will be different grades of lube oil and the bottoms will go to a coker unit, a cracking unit, an asphalt plant, or a heavy oil upgrading process. The light, medium and heavy lubricating oils are drawn off the tower through side-draws. The products of vacuum distillation include:
- Light Vacuum Gas Oil (LVGO)
- Heavy Vacuum Gas Oil (HVGO)
- Distillate Feedstocks for Lubricating Oil
- Vacuum Residuum
The bottoms are pumped through another furnace and into a second vacuum tower, sometimes called a vacuum flasher.
As the residuum enters the vacuum flasher, the lighter components flash into vapor and rise through the column. These lighter fractions are condensed using reflux streams and are drawn off as catalytic cracker feed. The vacuum flasher bottoms are drawn off and used as feedstock for the coker unit and the asphalt plant.
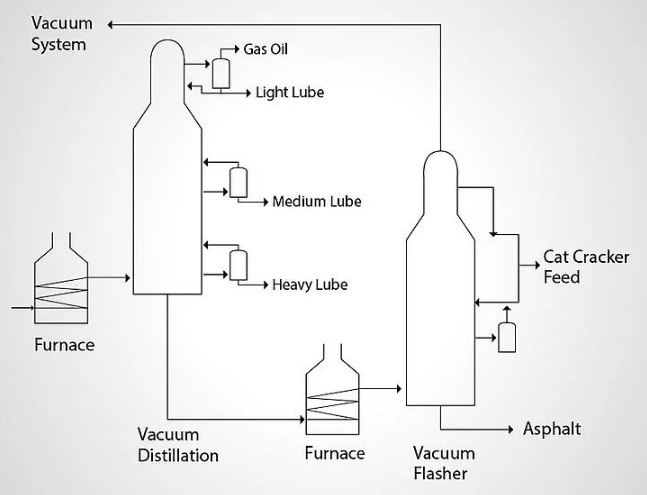
The deposits in crude unit will vary from the coke on the preheat bundles to iron sulfide with light oils in the atmospheric tower overheads to heavy lube oils and asphalt in the vacuum tower. This is why vacuum tower decontamination needs to occur. Most refiners are already set-up to circulate hydrocarbon solvents through-out the system and to steam-air decoke the furnaces. The low heat areas such as the towers can be cleaned successfully with chemicals added to a hydrocarbon solvent circulation. For light oils, water-based chemicals in a water solution can de-oil the system. The light product condensers will contain iron sides with light organic coatings and the heavier ends will be asphaltenes and tars.
Metallurgies will vary from carbon steel to stainless steels to monels. Depending on which types of crudes are being processed, there will exist the potential for naphthenic acid corrosion, hydrochloric acid corrosion, hydrogen sulfide corrosion, sulfide penetration, polythionic acid corrosion and erosion; so you need to be aware of the conditions of these units before treating with any aggressive chemicals. In general, the lighter the product the more likely the probability for corrosion.
The vacuum towers will become fouled with a mixture of organic and inorganic deposits. Given that the feed to the vacuum tower is from the bottom of the atmospheric tower, the organic deposits are usually asphaltenes, medium lube-grade oils and lighter end gases that have been trapped within the heavier oil components.
As these systems must be periodically cleaned to maintain product quality and process efficiency, the crude unit is taken out of service at great expense to the refiner. The expense to the refiner includes the loss of production, so completing the outage in the least possible time is critical. Maintenance work cannot begin until the equipment is decontaminated and safe for personnel entry.
Both the vacuum distillation and the vacuum flasher towers can be successfully cleaned using a solvent circulation and an oil-soluble chemical to expedite the cleaning process. The hydrocarbon solvent used as the carrier solvent for the chemical additive can be LVGO or even HVGO. If properly chosen, the chemical additive can reduce the heavy asphalt dissolution time by over 50% over use of a circulating hydrocarbon solvent alone. Additionally, this chemical additive can also suspend the asphalts for long term retention in liquid form and prevention of asphalt fouling in transfer feed lines and fouling of heat exchangers. The chemical additive can save the refiner much decontamination time and expense.
The towers, piping and heat exchangers can be circulated with a cascade method circulation with a hydrocarbon fluid containing the chemical additive to clean-out most, if not all, heavy deposits through a single circulation loop.
Removal of the resident heavy oils and asphaltenes is the first step in vacuum tower decontamination.
Following removal of the heavy deposits, the towers must be degassed of the light end hydrocarbon vapors prior to vessel entry. This is done by conventional vapor-phase degassing processes that have been previously discussed in this series.
There are new developments in the world of chemistry that can enhance the critical decontamination process and reduce the time required to successfully accomplish clean, safe equipment. Contact us for more information.