Contaminants
Asphaltene Control
Asphaltenes are one of the most common foulants in the industry, but have some of the largest impacts on production throughput, efficiency, and product quality.
Why are Asphaltenes a problem?
Asphaltene Control with FQE® Solvent-H+
Current Industry Practices
Why are Asphaltenes a problem?
Because of the high relative densities, asphaltenes precipitate out of crude oil in storage. The solids form a layer of tacky, gummy sludge on the bottom of the storage tank that grows over time and eventually must be removed.
The tank cleaning process is typically long and difficult and results in large volumes of hazardous waste that must be disposed at a hazardous landfill or incineration at a very large cost to the client. Asphaltenes also deposit in process equipment such as desalters, tower bottoms, and heat exchangers.
These deposits can create process inefficiencies including heat transfer losses and process upsets, and are typically removed by mechanical methods such as hydro-blasting. All of this is a maintenance expense and a production loss to the customer.
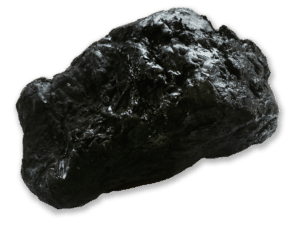
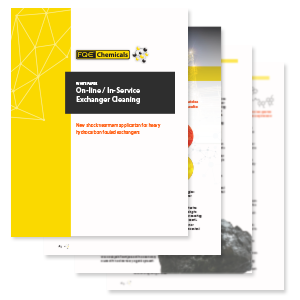
White Paper
On-line/In-ServiceExchanger Cleaning
Learn about a new shock treatment application for heavy hydrocarbon fouled exchangers.
Asphaltene Control with FQE Solvent-H+
FQE Solvent-H+ functions to dissolve asphaltene solids and then suspend the asphaltene in solution for long periods of time. The dispersion process prevents the asphalt molecules from re-agglomerating into larger masses that will quickly separate from the liquid as a solid.
While it is a dispersant, FQE Solvent-H+ also works as a solvent to dissolve the asphaltenes. While any aromatic solvent can dissolve asphaltenes, they do not suspend asphaltenes, leaving the asphalt to re-precipitate out of the solvent and form a hard layer of asphaltenes in a vessel.
Video Description
This experiment was set up to determine the efficiency of asphaltene dissolution using FQE Solvent-H versus two industry alternatives and water. As evidenced in the experiment, the soluble asphaltene was completely dissolved with vapor phase application of FQE Solvent-H. The alternatives tested essentially yielded the same results as using water (steam).
At the end of an hour, when only insoluble coke remained in the FQE beaker, a spatula was used to easily remove particulates from the beaker wall. FQE Solvent-H condensate was then transferred with the spatula to the other three beakers. The powerful active ingredients of FQE Solvent-H, in condensate, was able to solubilize the deposits in the remaining beakers.
In essence, the experiment mimics decontamination of vertical vessels using a vapor phase cleaning technique. The asphalt along the side of the beakers represent heavy fouling of vessels and process equipment, easily addressed by FQE Solvent-H. This video was shot in the FQE Chemicals Lab in Deer Park, Texas.
FQE Solvent-H+ is a non-combustible liquid with a flash of over 116°C (240°F). It is intended to be applied at concentrations ranging from 2–20% in a carrier hydrocarbon liquid. In a typical refinery application, FQE Solvent-H+ would be diluted in light cycle oil (LCO), atmospheric gas oil (LGO), light vacuum gas oil (LVGO), or diesel oil. Any of these hydrocarbon streams is acceptable as the carrier fluid for FQE Solvent-H+ application. This mixture is heated to 60 – 82°C (140-180°F) and circulated in the vessel or through piping.
How Does FQE Solvent-H+ Help?
FQE Solvent-H+ dissolves asphalt. It can remove fouling deposits in process equipment and restore system efficiency. It also removes heavy deposits in oil storage tanks. This yields two very important results: it lowers disposal costs, and eliminates the need for personnel entry into a confined space, which results in a much safer tank cleaning process.
FQE Solvent-H+ is valuable for its capability to dissolve asphaltenes. But many other solvents, like xylene, can dissolve asphaltene, too. What sets FQE Solvent-H+ apart is its asphaltene dispersion capability. By preventing asphaltenes from re-precipitation, the dissolved liquids not only eliminate a disposal expense, but become a valuable recovered hydrocarbon source, which can be reintroduced into the refining process without concern. No catalyst poisons. No process upsets.
Current Industry Practices
In general, refineries use hot solvents like diesel to flush / dissolve asphaltenes from equipment. The solvent / dissolved solids are put into storage, where the asphaltenes precipitate out as a solid that must be addressed later. The flushing process never removes all of the asphalt deposits. The residual asphalt is mechanically removed in the pre-maintenance cleaning. For storage tank accumulations, the asphalts are mined out with bulldozers for disposal.
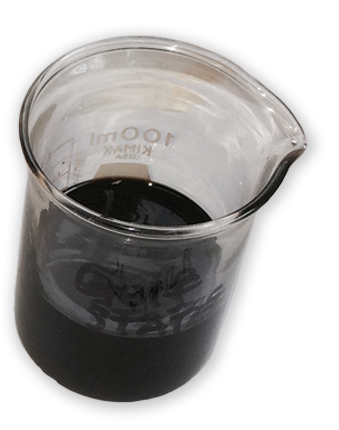