Case History
Vacuum Tower Turnaround Success
Clean in Place – No Equipment, No Contractors, No Waste
Challenge
A vacuum tower needed to be cleared and cleaned of asphaltenic solids, H2S and pyrophoric iron.
Solution
Added FQE Solvent-H+ into once through flush to the coker
Circulated coker gas oil with Solvent-H+ for 8-hours through VTB and heavy gas oil circuit
Results
- Packing which previously needed jack hammering to be removed came out easily
- >85% decrease of VTB on seal pan with only ½-inch of soft residue remaining
- Cleaned heat exchangers at the same time
- Handled internally by client
- No waste
Products
TAR of Vacuum Tower
Circulation of the unit with Solvent-H+ added to coker gas oil proved successful in dissolving the asphaltenic foulant and exposing and removal of the embedded pyrophoric iron. All resolved material was rerun through the process; thus, generating no waste.
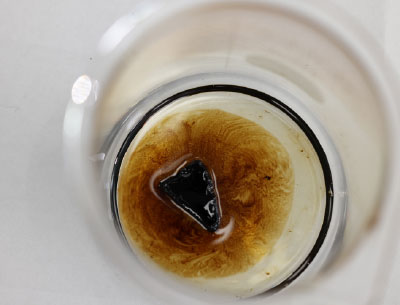
Vacuum Tower Turnaround
Vacuum towers grapple with a host of challenges stemming from the accumulation of heavy asphaltenic hydrocarbons and pyrophoric iron sulfide within the intricate structure of the tower. The packing, valve trays, and bubble cap trays serve as prime sites for these undesirable deposits to accumulate. In this case, the feedstock was heavy Canadian crude, further intensifying the issue. The severity of the asphaltene problem is exacerbated by an API gravity below zero. These contaminants persist and age over time, becoming firmly baked onto the surfaces during regular, years-long operations. Adding to the complexity, the pyrophoric iron can be embedded within the asphaltenes. Thus, removing the asphaltenic binder becomes imperative to expose the pyrophoric iron, effectively mitigating and neutralizing the ignition source.
Solvent-H+ is Solvency Power
Using typical cutter stocks, like diesel, will have limited potential to dissolve to remove the asphaltene. The unit is designed to separate these two. The simplistic like-dissolve-like phrase provides some guidance here. Using a linear alkane diesel to solubilize an aromatic asphaltene will have limited capacity.
Simultaneous Cleaning
FQE Solvent-H+ was introduced into the cooling once-through pass that was feeding the coker. This simultaneous cleaning and deposit removal process significantly minimized critical outage time. Following a circulation period of 8-hours with the addition of Solvent-H+, even in challenging scenarios involving the heat exchanges, proved to be effective. This approach not only ensured thorough cleaning of the tower and heat exchangers but also generated substantial time savings while generating no waste. Given the utilization of opportunity crudes and the inherent difficulties in separating these heat exchangers bundles, due to freezing or being stuck in place, this method proved to be particularly advantageous for the refinery.
Make the Right Choice
The advantages of employing this innovative cleaning technology are manifold. Firstly, it facilitates the removal of stubborn, heavy asphaltenic deposits within the tower without the need for labor-intensive jack hammering or water blasting. This not only expedites the process but also ensures a smoother operation overall. Additionally, the circulation duration can be closely monitored, thanks to a distinct endpoint, enabling a more efficient workflow.
Furthermore, the cleanup process is simplified, demanding less effort and time on critical path operations, and because this can be carried out by the owner without the need for third-party contractors or opening piping to add fittings, it greatly reduces man-hours involved. Lastly, it prioritizes safety, providing a secure and reliable method for the removal of deposits within the tower with less confined space entry.
Following this step with vapor phase cleaning utilizing other FQE products, LEL-Surface and Pyrophoric, would complete the process before confined space entry.