Part 4
Part 4, focusing on atmospheric distillation fouling, in the series on how the chemical industry is solving challenges in the industrial sector.
The first major process in the refining of petroleum is the distillation of the crude oil at atmospheric pressure. The products of atmospheric distillation include:
- LPG and lighter gases
- Straight-run gasoline
- Naphtha
- Gas Oil
- Fuel Oil (kerosene)
- Atmospheric Residuum (bottoms/asphalt)
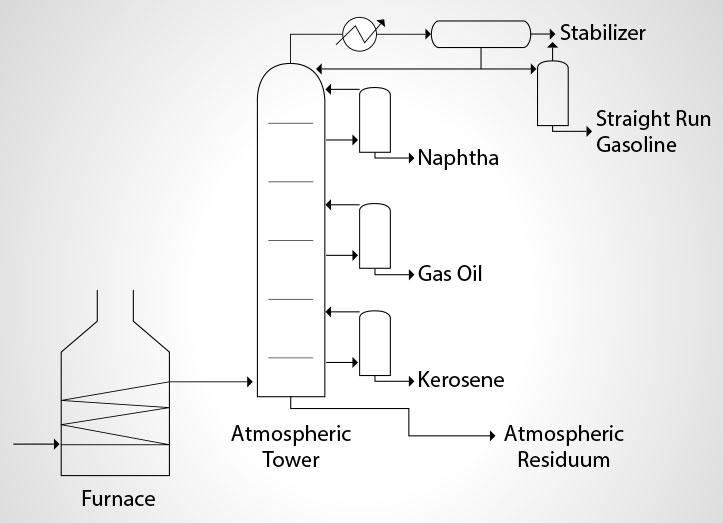
Atmospheric Distillation Process
Distillation is a process by which a desired product is separated from other components of a feedstock. The distillation process takes advantage of the difference in the boiling points. As heating of the feedstock occurs, it reaches the boiling temperature of some of its lighter components. The lighter components are flashed-off as vapor from the heavier components.
First, the feed heats to the point where it is a mixture of liquid and vapor. As the feed mixture enters the tower, the liquid falls to the tower bottom and the vapor rises to the top of the tower. To provide for effective heat transfer in the tower we must use a method to promote contact between the rising vapors and the falling liquids. The tower trays serve this purpose. Inside the tower are a series of trays that have perforations in them. These perforations allow the vapors to rise. The trays typically use a device called a bubble cap. The bubble cap will force the vapor to “bubble” through a layer of collected liquid that is several inches deep on each tray.
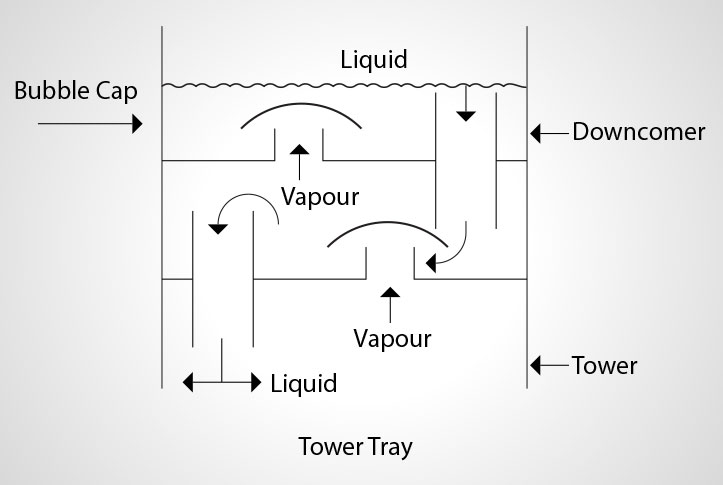
As the vapor rises through the liquid, it transfers some of its heat to the liquid. This heat transfer causes the vapor to cool slightly and some of the heavier components of the vapor to condense into a liquid. The reverse is also true. As the liquid on the tray gains heat from the vapor, some of its lighter components are driven off as a vapor. The vapor rises up to the next tray and the process repeats.
Atmospheric Distillation Fouling
Proper operation of a distillation tower (fractionator) depends on the heat transfer from the vapor to the liquid phase. Tower trays, particularly those in the lower portion of the tower, have a tendency to form foulants. The degree of fouling is enough to interfere with the operation of the tower and the quality of the separated products. When this happens, tower cleaning must occur.
Tray fouling leads to a poor contact between vapors rising through the tower and the liquid. Overhead condenser fouling can reduce the amount of refluxing that takes place – which can reduce the quality of the overhead products. Reboiler fouling increases the cost of fuel required to operate the unit.
Atmospheric distillation fouling comes in several types. The type of fouling is primarily a mixture of organic and inorganic deposits that can be heavy in iron content. The lower tower trays will have heavy organic deposits, primarily waxes and asphaltenes. As we move to kore and more heavier crudes that are sour (high in hydrogen sulfide content), we also encounter pyrophoric iron scales. These occur inside the upper region of the tower. Addressing the scales is essential, as it prevents a potential fire. This is mandatory before vessel entry and before manual maintenance work can begin.
The atmospheric tower fouling decontamination process during a shutdown is a critical path item as maintenance work is dependent on its expedient success. Outage time costs the refiner hundreds of thousands of dollars in lost revenue from lost production time. The tower undergoes degassing of vapors, cleaning of residual liquids, and removal of solid organic deposits. Additionally, neutralization of dangerous hydrogen sulfide and combustible iron sulfide scales takes place. All of this must be successfully completed in the least amount of time possible.